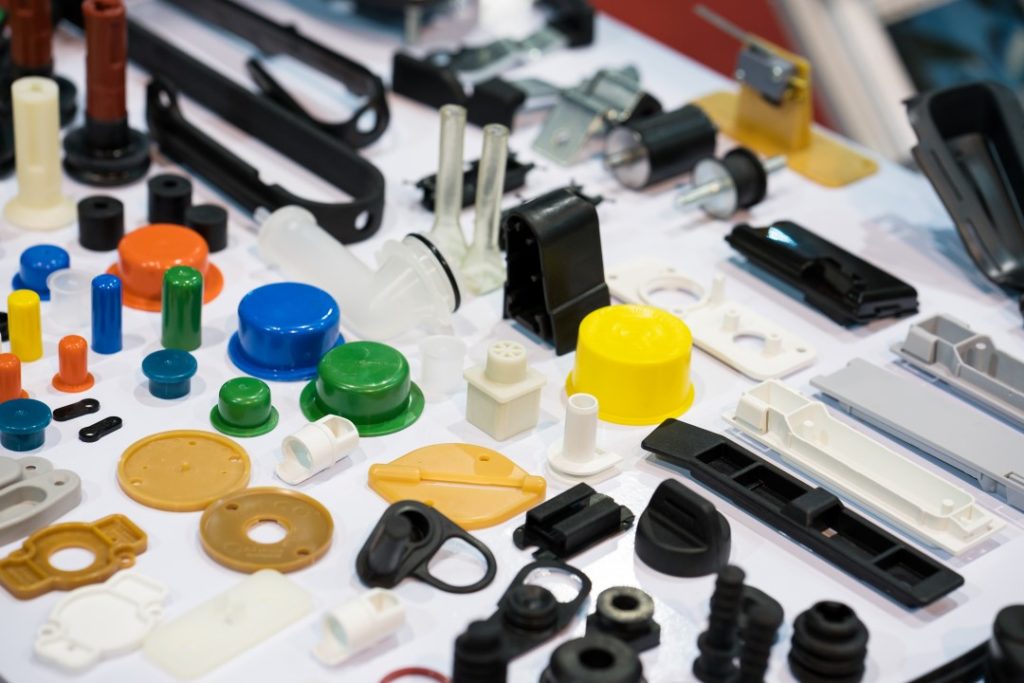
What is Plastic Injection Molding?
Plastic injection molding uses custom-made, precise tooling molds to mass produce identical plastic models that meet your exact shape and size specifications. The key to getting consistent results is the custom tooled molds, which are carefully and meticulously engineered from high-quality materials, usually aluminum or hardened steel, that can withstand repeated exposure to high temperatures and pressures. These molds can be used to produce millions of products that are all exactly the same.
The injection molding process is straightforward. Once the custom injection mold is designed and approved, raw plastic, resins, and other materials are heated to the most efficient injection temperature. High-pressure tools then inject the plastic into the mold at rates specified to achieve the best result. The plastic product is then cooled and removed from the mold. Once the product passes QC, it’s ready for packaging and transport.
Plastic injection molding is one of the most widely used mass manufacturing methods. It produces high volumes of solid plastic products and components rapidly, reliably, and cost-effectively. Examples of plastic injection products include the following:
- Gears, pulleys, washers, and brackets
- Enclosures
- Robot parts
- Front panels
- Toy parts
- Knobs
- Packaging
- Appliance parts
- Power tools
- Electronic enclosures
- Valves
- Automotive components
- Airplane parts
- Containers
- Water bottles
Objects made using plastic injection molding are everywhere!
Advantages and Disadvantages of a Plastic Injection Molding Company
The number one advantage of producing your products with a plastic injection molding company is economies of scale; because the molds and machines set up can be used to produce high volumes of parts, the cost per unit is very low. Beyond that, other advantages include the following:
- Low scrap rates. Very little material is wasted during injection molding.
- Consistency. The second part you produce using injection molding, the 100th part, and the 1,000,000th part will all be identical to the first. This consistency and reliability are invaluable to creating a solid brand.
Plastic injection molding has a few downsides that are important to consider. First, upfront costs tend to be high. Getting the design and tooling right takes considerable resources. It also takes time, which is the second disadvantage of the process. Lead times to introduce a new product can be significant. Third, changes to the design can be difficult to make and it’s not always possible to simply tweak a mold; some changes will necessitate starting over. And finally, plastic injection molding has size limitations. It’s not always feasible to mass produce large components using this method. You may need to produce several smaller parts and then bond them together to create larger items.
Despite these disadvantages, plastic injection molding continues to be a leading choice for mass production. Choosing a reputable, experienced plastics company will help you harness the advantages and minimize the downsides so you can get the maximum value from the process.
Plastic Manufacturing Services that Matter
When choosing a plastics manufacturer to work with, it’s important to consider the following capabilities:
1) Variety of Product Offerings
The plastic injection molding company typically will provide manufacturing support for a wide range of products, including the following categories:
- NSF Certified Products like soft drink fountain components
- Automotive/Motorcycle Products like taillight, turn signal lenses and housings, fuse holders, speaker brackets and assemblies, and RV components
- E.M. Products like fuse pullers, circuit and voltage testers, vending machine parts, point of purchase display components, computer cases, and components
- Consumer Products like camera cases, glasses, flowerpots, toys, clock parts, telephone internal parts, timers, and scale parts
- Medical, Non-Intrusive Products like unit dose medicine packaging and many other convenience containers designed to meet a specific storage need or application.
Your partner needs to be able to provide the right services for your product.
2) Part Design and DFM (Design for Manufacturability) Services
Mold design and tooling represent both the biggest opportunities for your product and the greatest challenges. Getting the design right results in a process that will serve you well over the product’s entire life cycle. But getting that design right is a critical project in itself and your plastics company and their DFM services can help.
DFM is successful when the plastics manufacturer and the design engineers combine their expertise to formulate the optimal materials and tools. Focusing on key aspects of the design and production process from the beginning results in significant upfront savings such as the following:
- DFM simulations help you optimize your mold and tooling, resulting in fewer expenses relating to changing, repairing, or scrapping prototype molds.
- DFM simulations help engineers optimize flow rates, pressures, and cooling times, resulting in shorter cycle times and less waste.
- DFM helps you get a tight design that minimizes resin content, maximizes structural integrity, and lowers your part count, leading to lower material and assembly costs.
- DFM helps you get things right the first time, helping you get your product to market quickly.
Your plastics manufacturer is an important partner in bringing your design to life and in helping you build an efficient production process that allows you to enjoy all of the economic benefits of plastic injection molding.
3) Production, Assembly, and Fulfillment
The best plastics companies have highly skilled team members specializing in every aspect of production, assembly, packaging, distribution, and tooling. Ask the following:
- Can the manufacturer support the production volume you require?
- Do they provide secondary services such as trimming, hole drilling, assembly, and packaging?
- Do they have the ability to store inventory and ship on demand?
- Does the manufacturer have a proven track record and positive long-term relationships with clients?
Choose JB Plastics, Inc. as your Plastic Injection Molding Company
JB Plastics, Inc., is a full-service plastic injection molding company located in the Orange County, California area. Our teams provide comprehensive services, including DFM services, product design, mold design, long-run and short-run production, and fulfillment. JB Plastics is the only resource you need for plastic injection molding services. Contact our team today to see what we can do for you! (714) 541-8500